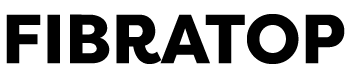
Concrete fibers: glass, polypropylene, and steel fibers
Although concrete is a material that enjoys exceptional mechanical and chemical properties, it is advisable to reinforce it to further enhance these capacities.
In this sense, concrete fibers are the perfect complement to achieve this goal. They provide extra tensile strength to the structure. This reduces the chances of cracking, the effects of shrinkage during curing, and exponentially increases impact and fatigue resistance.
Concrete fibers have been designed to replace the use of mesh, thus changing traditional application systems to more modern and faster ones to execute.
Types of concrete fibers and their differences
The most common types of concrete fibers today are glass fibers, polypropylene fibers, and steel fibers. At Topciment®, we offer all three types so that professionals can choose according to their preferences. For stamped concrete, the most commonly used fibers are polypropylene fibers.
Broadly speaking, the most relevant differences lie in workability, cracking and abrasion, corrosion, and exposed ends.
Workability
While glass fibers require the addition of extra additives to facilitate their mixing with concrete, polypropylene fibers and steel fibers are simpler and more convenient as they do not require such additives.
Abrasion and Cracking
Concrete fibers, regardless of the material they are made of, contribute to improving the mechanical strength of structural elements. In other words, their purpose is to reduce possible cracks and fissures. However, steel fibers and glass fibers are more resistant to abrasion.
Corrosion
In this regard, polypropylene fibers stand out for providing greater resistance to corrosion. The difference is quite significant, as steel fibers, for example, are more prone to corrosion.
Exposed Ends
When fibers are mixed with concrete, there is a risk that the ends of the filaments may remain exposed on the surface. Hence, the importance of choosing appropriately. Polypropylene fibers and glass fibers are the most reliable in this regard, as this issue does not occur. On the other hand, steel fibers may leave some ends exposed.